Our projects
The production of vegan cheese slices initially yielded a product quality rate of only 68%. To address this, a comprehensive set of root cause analyses of the defects was conducted, followed by the implementation of a variety of targeted improvement initiatives. A key strategy involved integrating two critical production steps and precisely controlling the cooking process parameters under zero atmosphere conditions. This entailed making mechanical engineering modifications to existing equipment, as well as installing newly designed equipment to achieve the desired operating conditions (Top left figure).
I also standardized the cooking procedures, updated the work instructions, and provided extensive training to the operations team. These enhancements led to a remarkable 28% increase in product quality, generating a cost savings of $2.8 million over two years.
The significant enhancement in product quality not only elevated the consumer experience but also bolstered the brand's reputation. This improvement paved the way for the brand to attract and secure partnerships with larger retail and quick service restaurant customers.
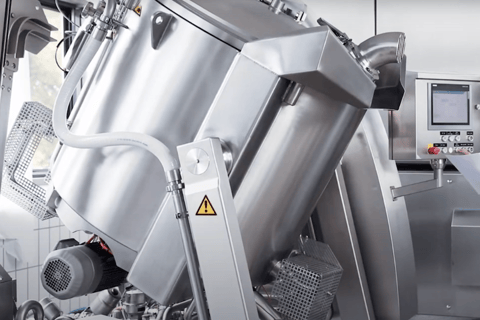
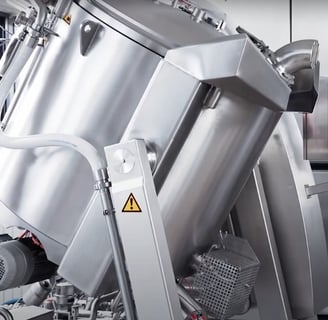
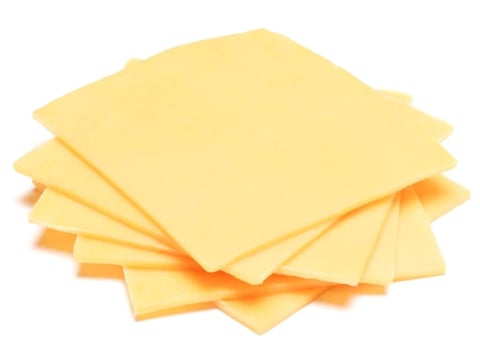
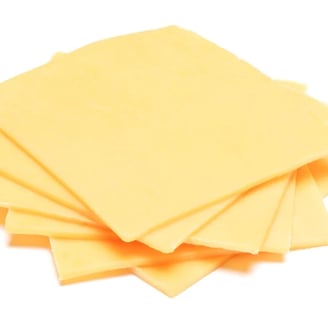
Vegan Food Manufacturing
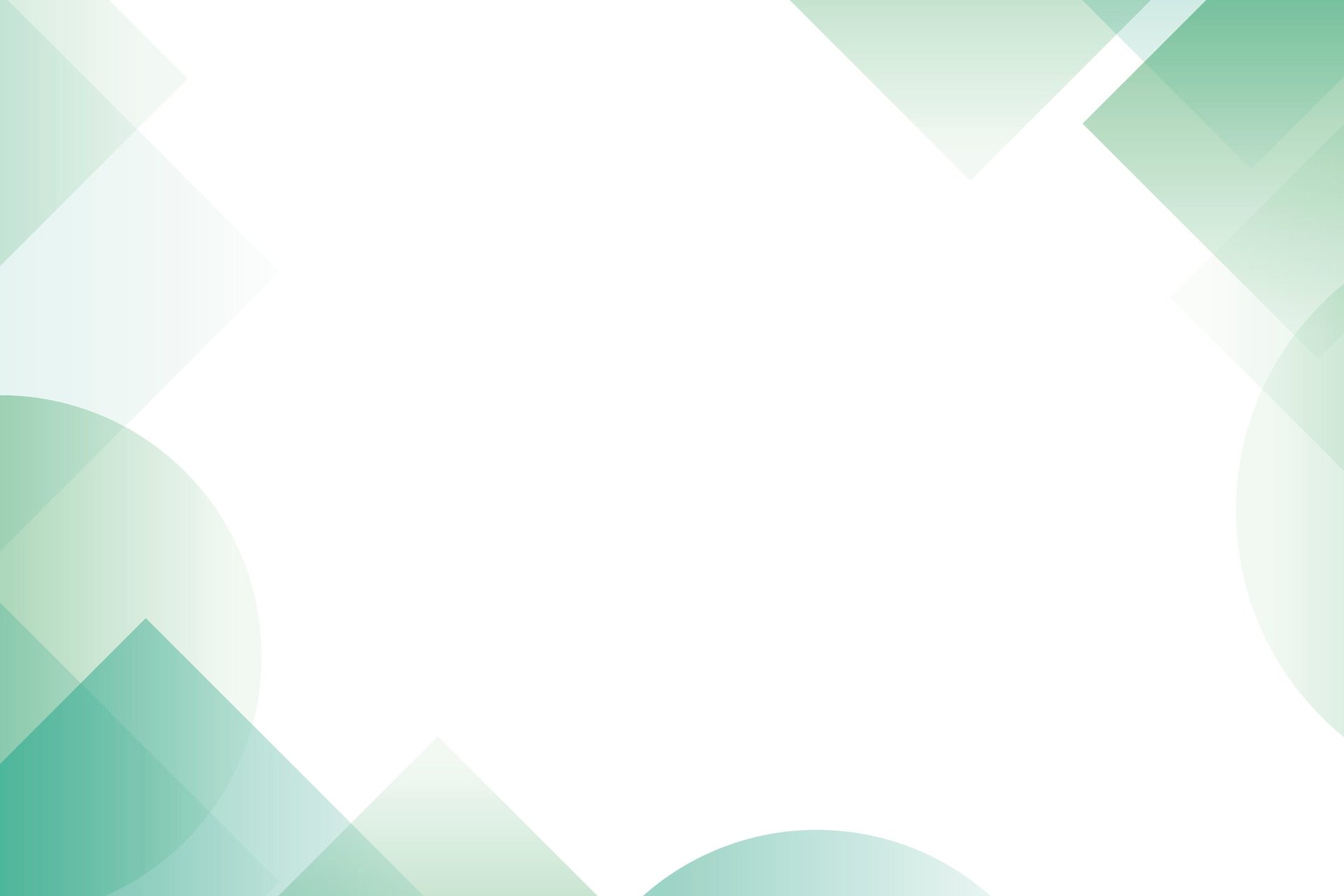
I implemented a cutting-edge real-time performance monitoring system on high-speed manufacturing and packaging lines. This work involved installing laser photo-eye sensors and integrating signals from the machine PLCs. The collected data was consolidated into a data warehouse and delivered through a SaaS platform, providing an interactive dashboard accessible on personal devices and iPads. This dashboard offered valuable insights into performance metrics and critical KPIs, essential for tracking operational efficiency.
As a result, the system significantly boosted the company’s Overall Equipment Effectiveness (OEE) by 43% and correspondingly reduced operational expenses. This system also empowered the supply chain team, specifically in demand planning, to more accurately monitor the progress of job orders and adjust their plans in real time.
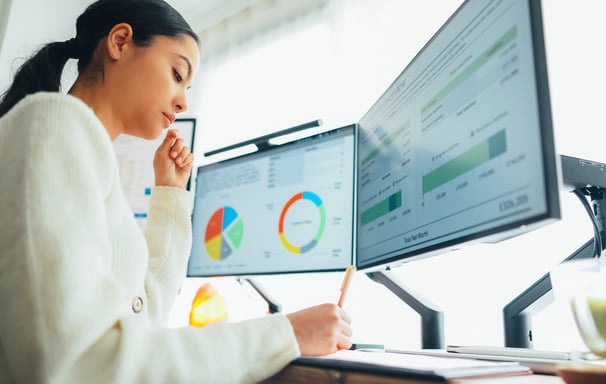
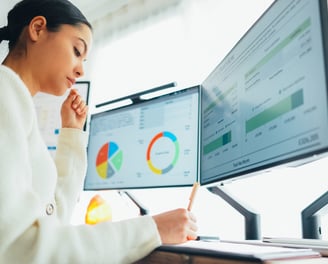
Data Analytics
Each phase of the drilling process was meticulously optimized to eliminate the 7 LEAN wastes. I conducted an in-depth step-time analysis to identify instances of waiting, excessive motion, over-processing, and unnecessary transportation throughout the process. Following this, a 5-WHY analysis was performed to uncover the root causes of time losses and additional processing.
Based on these insights, I developed a streamlined operational plan and strategically staged equipment to be more accessible, thereby minimizing non-value-added activities such as excessive motion and transportation.
These improvements led to a 31% reduction in the overall production lead time.
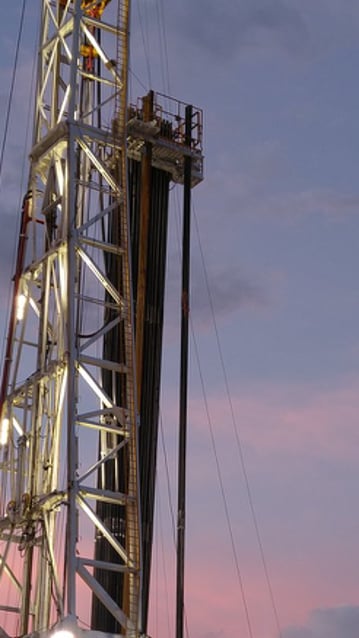
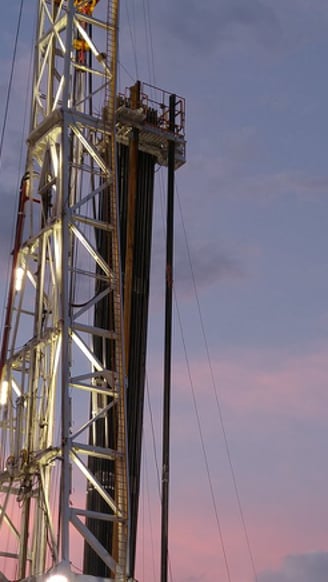